Enzyme Technology
Enzyme reactors
An enzyme reactor consists of a vessel, or
series of vessels, used to perform a desired conversion by enzymic means. A
number of important types of such reactor are shown diagrammatically in Figure
5.1. There are several important factors that determine the choice of reactor
for a particular process. In general, the choice depends on the cost of a
predetermined productivity within the product's specifications. This must be
inclusive of the costs associated with substrate(s), downstream processing,
labour, depreciation, overheads and process development, in addition to the more
obvious costs concerned with building and running the enzyme reactor. Other
contributing factors are the form of the enzyme of choice (i.e., free or
immobilised), the kinetics of the reaction and the chemical and physical
properties of an immobilisation support including whether it is particulate,
membranous or fibrous, and its density, compressibility, robustness, particle
size and regenerability. Attention must also be paid to the scale of operation,
the possible need for pH and temperature control, the supply and removal of
gases and the stability of the enzyme, substrate and product. These factors will
be discussed in more detail with respect to the different types of reactor.
Batch reactors generally consist of a tank
containing a stirrer (stirred tank reactor, STR). The tank is normally fitted
with fixed baffles that improve the stirring efficiency. A batch reactor is one
in which all of the product is removed, as rapidly as is practically possible,
after a fixed time. Generally this means that the enzyme and substrate molecules
have identical residence times within the reactor, although in some
circumstances there may be a need for further additions of enzyme and/or
substrate (i.e., fed -batch operation). The operating costs of batch reactors are
higher than for continuous processes due to the necessity for the reactors to be
emptied and refilled both regularly and often. This procedure is not only
expensive in itself but means that there are considerable periods when such
reactors are not productive; it also makes uneven demands on both labour and
services. STRs can be used for processes involving non-immobilised enzymes, if
the consequences of these contaminating the product are not severe. Batch
reactors also suffer from pronounced batch-to-batch variations, as the
reaction conditions change with time, and may be difficult to scale-up, due to
the changing power requirements for efficient fixing. They do, however, have a
number of advantageous features. Primary amongst these is their simplicity both
in use and in process development. For this reason they are preferred for small-scale production of highly priced products, especially where the same equipment
is to be used for a number of different conversions. They offer a closely
controllable environment that is useful for slow reactions, where the
composition may be accurately monitored, and conditions (e.g., temperature, pH,
coenzyme concentrations) varied throughout the reaction. They are also of use
when continuous operation of a process proves to be difficult due to the viscous
or intractable nature of the reaction mix.
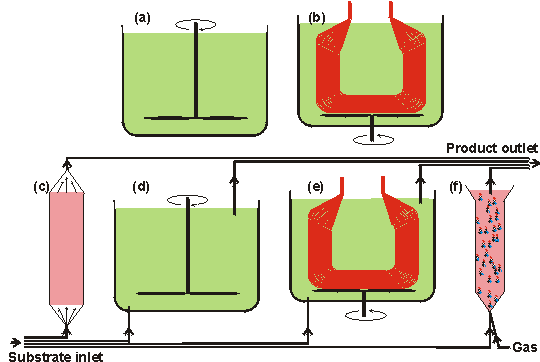
Figure 5.1. Diagrams of various important
enzyme reactor types.
-
Stirred tank batch reactor
(STR), which contains all of the enzyme and substrates) until
the conversion is complete;
-
batch membrane reactor (MR),
where the enzyme is held within membrane tubes which allow the
substrate to diffuse in and the product to diffuse out. This
reactor may often be used in a semicontinuous manner, using
the same enzyme solution for several batches;
-
packed bed reactor (PBR), also
called plug -flow reactor (PFR), containing a settled bed of
immobilised enzyme particles;
-
continuous flow stirred tank
reactor (CSTR) which is a continuously operated version of (a);
-
continuous flow membrane reactor
(CMR) which is a continuously operated version of (b);
-
fluidised bed reactor (FBR),
where the flow of gas and/or substrate keeps the immobilised
enzyme particles in a fluidised state.
All reactors would
additionally have heating/cooling coils (interior in reactors (a), and (d), and
exterior, generally, in reactors (b), (c), (e) and (f)) and the stirred reactors
may contain baffles in order to increase (reactors (a), (b), (d) and (e) or
decrease (reactor (f)) the stirring efficiency. The continuous reactors ((c)
-(f)) may all be used in a recycle mode where some, or most, of the product
stream is mixed with the incoming substrate stream. All reactors may use
immobilised enzymes. In addition, reactors (a), (b) and (e) (plus reactors (d)
and (f), if semipermeable membranes are used on their outlets) may be used with
the soluble enzyme.
The expected productivity of a batch reactor
may be calculated by, assuming the validity of the non -reversible Michaelis -Menten
reaction scheme with no diffusional control, inhibition or denaturation (see
reaction scheme [1.7] and equation (1.7). The rate of reaction (v)
may be expressed in terms of the volume of substrate solution within the reactor
(VolS) and the time (t):
(5.1)
Therefore:
(5.2)
On integrating using the boundary condition
that [S] = [S]0 at time (t) = 0:
(5.3)
Let the fractional conversion be X, where:
(5.4)
Therefore;
(5.4a)
and
(5.4b)
Also
(5.4c)
Therefore substituting using (5.4c) and (5.4b)
in (5.3):
(5.5)
The change in fractional conversion and
concentrations of substrate and product with time in a batch reactor is shown in
Figure 5.2(a).
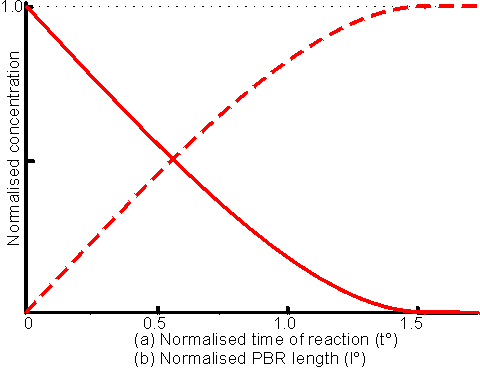
Figure 5.2. This
figure shows two related behaviours.
(a) The change in substrate and product
concentrations with time, in a batch reactor. The reaction S
P is assumed, with the initial condition [S]0/Km
= 10. The concentrations of substrate (———
and product (-----------) are both
normalised with respect to [S]0. The normalised time (i.e., t° = t Vmax/[S]0)
is relative to the time (t° = 1) that would be required to convert all the
substrate if the enzyme acted at Vmax throughout, the actual time
for complete conversion being longer due to the reduction in the substrate
concentration at the reaction progresses. The dashed line also indicates the
variation of the fractional conversion (X) with t°.
(b) The
change in substrate and product concentrations with reactor length for a PBR.
The reaction S P is assumed with the initial condition, [S]0/Km
= 10. The concentrations of substrate (———) and product (-----------) are both
normalised with respect to [S]". The normalised reactor length (i.e., I° =
lVmax/F, where Vmax is the maximum velocity for unit
reactor length and I is the reactor length) is relative to the length (i.e., when I°
= 1) that contains sufficient enzyme to convert all the substrate at the given
flow rate if the enzyme acted at its maximum velocity throughout; the actual
reactor length necessary for complete conversion being longer due to the
reduction in the substrate concentration as the reaction progresses. P may be
considered as the relative position within a PBR or the reactor's absolute
length.
Home
| Back | Next
This page was established in 2004 and last updated by Martin
Chaplin on
6 August, 2014
|